Risk Based Inspection (RBI) is a risk assessment and management process that focuses on loss of containment of pressurised equipment in processing and refining facilities, due to applicable damage mechanisms which cause material deterioration.
These risks are managed primarily through equipment inspection. By targeting high-risk areas, a recommended inspection plan (inspection effectiveness) can be implemented on complex systems to minimise unplanned shutdown(s), improving the integrity of the facilities by reducing loss of containment. The implementation of an RBI program, however, can be is challenging.
In this new insight, Ashfaq Ali, Senior Asset Integrity Engineer at Penspen, explores key organisational challenges and offers practical solutions for effectively implementing a Risk-Based Inspection (RBI) program in oil and gas facilities. With over 16 years of experience in asset integrity, corrosion management, and RBI, Ashfaq specialises in optimising asset integrity programs and mitigating risks across both onshore and offshore operations.
1. Implementation Team
The successful implementation of RBI requires a skilled team that has experience in managing equipment failure modes, inspection methods, and understands government regulations. Skill shortages and a lack of personnel with appropriate depth of expertise can adversely impact RBI program implementation.
Solution: Provide training to new and current staff for RBI methodology and principles. Familiarise inspectors, engineers, and risk managers with the technical and analytical specifics of RBI. If required, outsource the service to an organisation specialising in RBI to ensure appropriate program establishment and implementation..
2. Scope of Work (SOW) Understanding
SOW understanding is crucial for an effective RBI program – without an in-depth, detailed discussion of the scope, the procedures required, and a defined inspection plan, any chance of the project being a success is reduced. The old adage ‘fail to plan, plan to fail’ comes into play, with underdeveloped understanding or failure to perform the proper studies needed to fully lay out a complete scope of work for the plant or asset causing potential delays and risking project success.
Solution: Conduct workshop with all the team members from operation, process, and inspection departments to screen down the assets which really no need to include in RBI assessment.
3. Limitations of RBI Methodology
If the RBI methodology has not been fully understood and well documented, it may lead to either over-conservative or non-conservative results, and sometimes the RBI assessment generates the worse results due to the lack of understanding the methodology. For example, if small-bore piping systems are clubbed with large diameter piping for an RBI analysis, it can lead to non-conservative results for the smaller ones.
Solution: Learn detailed information about your chosen RBI methodology calculations and their assumptions before starting the RBI program. Should have the idea that how each input parameter does affect the results related to risk calculations and inspection strategies.
4. Data Quality
RBI assessment results are heavily dependent on accurate and comprehensive data (e.g. equipment history records, process conditions, failure modes etc.). Incomplete or low-quality data can lead to inaccurate risk estimates. In turn, any results will also be inaccurate.
Solution: Maintain and implement a robust data management system to centralise and standardise data collection. On site meetings and interviews with operations, maintenance, and engineering groups are critical to ensure accurate data intake.
5. Damage Mechanism Reviews
The review of damage mechanism is a mandatory element of a risk-based inspection assessment and a main area of development for an effective mechanical integrity program. If the implementation team does not perform a comprehensive review of damage mechanisms based on the true parameters for damage calculations, any risk analysis results may be compromised which further affects inspection strategies.
Solution: A competent corrosion engineer can aid an implementation team in developing a strategy where condition monitoring locations (CMLs) are assigned on a vessel or on a pipe to focus on areas where damage is most likely to be encountered, making RBI effectively applied to the piping circuit and pressure vessels.
6. Validation of Assumptions Taken
For every RBI assessment, basis and assumptions are established for some missing information and non-availability of some input parameters. Sometimes these assumptions are made so conservatively that the true benefits of RBI assessment are not realised. So, validation of such assumptions is critical for the successful assessment of RBI.
Solution: Validate the assumptions taken with concerned teams (operations, process, and inspection) from the facilities to enhance the effectiveness of the RBI assessment.
7. Software Selection
Choosing a suitable RBI software can be challenging. Any software must be compatible with organisational needs and capabilities, easy to integrate with existing systems, up-to-date with the latest industry standards, and user-friendly for those implementing the program.
Solution: Conduct thorough market research and compare RBI software packages in terms of functionality, ease of use, and compatibility with existing systems. Involve end-users in the selection process to ensure the tool meets their needs. Consider cloud-based options for scalability and access. Make sure the software allows for customisation and updates as the RBI program changes.
Conclusion
RBI program implementation requires a combination of technical competency, comprehensive methodology, team collaboration, and understanding of risk results. By enhancing data quality, building a risk-based decision-making culture, and leveraging technology, organisations can effectively implement and sustain an RBI program that enhances safety, reliability, and operational efficiency.
Penspen is well-equipped to support the successful implementation of RBI programs. With a team of highly skilled professionals and a strong track record in delivering RBI solutions, we have successfully assisted leading oil and gas operators and EPC companies worldwide. Our proven track record includes implementing RBI programs for one of the largest refineries globally, demonstrating our capability in delivering high-quality, industry-leading solutions.
Related Insights
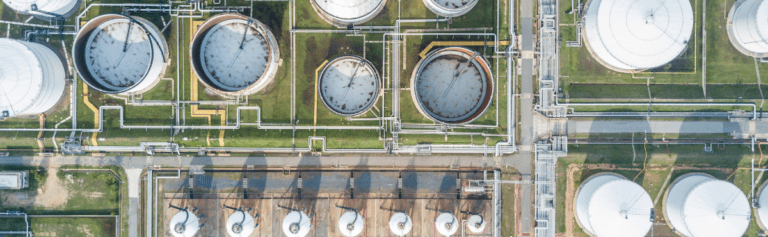
Overcoming the Challenges in Implementing a Risk-Based Inspection (RBI) Program
Risk Based Inspection (RBI) is a risk assessment and management process that focuses on loss of containment of pressurised equipment in processing and refining facilities, due to applicable damage...
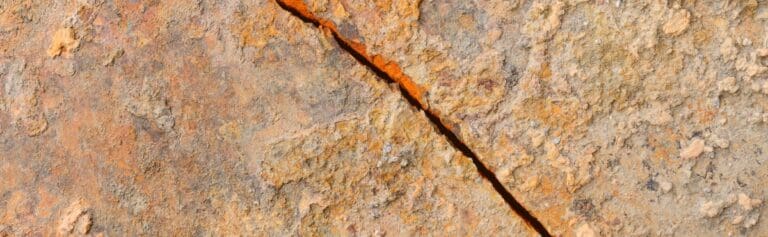
Demystifying Hydrogen Fatigue Crack Growth
With the increasing momentum to adopt clean fuels coupled with the scrutinised investment horizons of maintaining ageing gas pipelines, there are well-established and mutually beneficial...
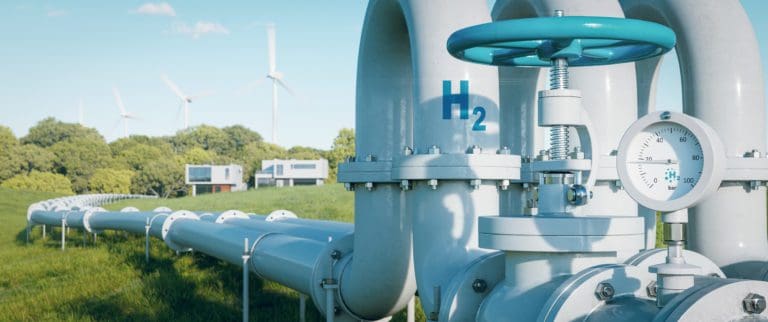
What Are the Key Integrity Considerations When Repurposing Pipelines for Hydrogen?
With the European Hydrogen Backbone targeting 52,000 km of hydrogen pipelines by 2040 - 60% of which will be repurposed from existing infrastructure - ensuring the integrity of these pipelines will...
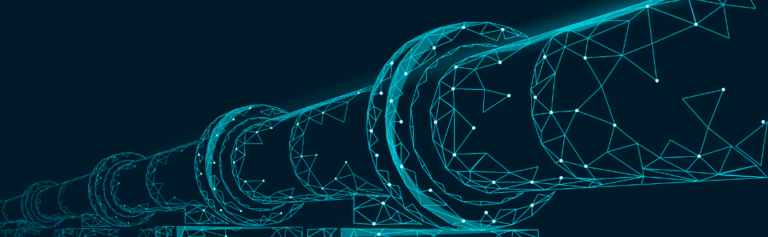
Beyond Compliance: Optimisation Opportunities of the Gas Mega Rule – Pipeline Integrity Management with Digital Twins, Multiple Inspections, and Artificial Intelligence
In a new technical paper presented at the 2025 Pipeline Pigging and Integrity Management Conference, Penspen, Senslytics, and PipelineLogic explore how Penspen's THEIA platform and Causal AI...